
“It’s not something we take lightly,” Woolcock said. There’s a reason why so few makers offer their own forks and that’s because bad things happen when things go wrong. Bastion has created in-house test equipment to perform the required durability and strength tests. Test equipment was built and the idea soon came to reality. The fork and cockpit was a project Bastion started two years ago, but some forced time away from manufacturing (almost 100 days) during last year’s extensive coronavirus lockdowns in Melbourne gave the team plenty of time to focus on the development. The exact process was hush-hush, but they were proud of the consistent lay-up compaction achieved. Bastion is using pre-impregnated carbon fibre for the legs and steerer of the fork, and crossbar of the bar-stem. With such an investment it just makes sense that Bastion would grow its product offering and complete the unique look of its frames. “Literally titanium powder and raw carbon fibre come in the front door, and the fork and cockpit go out,” Woolcock said. They have not one, but two 3D titanium printers, and new facilities to produce carbon components themselves that goes beyond the previous filament-wound products, too. By doing our own fork in-house, we can specify exactly what fork rake we want.”Īdding to that, Bastion has made some significant investments in its ability to manufacture in-house and control the process. “We get the benefit of doing custom geometry and not being beholden to purchase in a fork that then limits us in fork rake selection. got completely hidden integrated cables,” said Woolcock of the new fork, bar, and stem combination that’s compatible with the company’s existing disc road bikes. “From a functionality point of view we had a lot of customers asking about integrated cables. The new system provides a clean and unmistakably-Bastion aesthetic. Bastion intends to keep offering its bikes with those off-the-shelf products for customers who want exposed cabling or have a specific bar/stem they love, but there was also room for improvement – by creating a front end that employs the same customisable and lattice-structured titanium lug concept as its bespoke framesets.
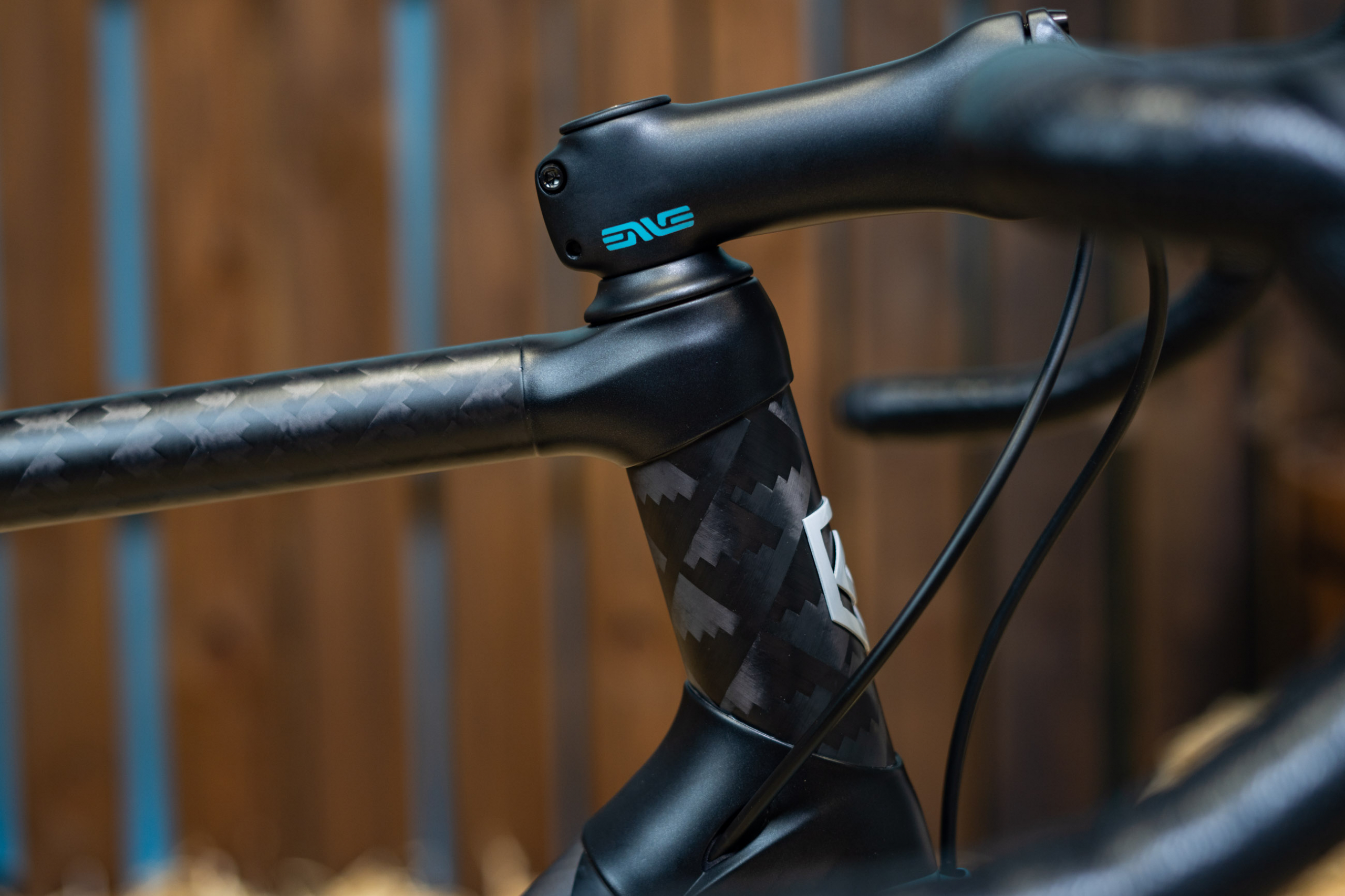
Why make a fork and cockpit?īastion has been making frames with 3D-printed titanium lugs and carbon tubes since 2015, and until now had relied on the likes of Enve and THM for supply of forks and cockpits. The cranks and handlebars will be available to order starting in January 2020.Heading out the door? Read this article on the new Outside+ app available now on iOS devices for members!īest known for its custom 3D-printed titanium lug and carbon tube frames, Bastion Cycles is now using that technology to offer an integrated, matching and wholly made-in-house disc road fork, stem, and bar.ĭuring a factory tour (more on that soon) the day before the Handmade Bicycle Show Australia, CyclingTips sat down with Bastion co-founder and lead engineer James Woolcock to learn about this new product segment for the Melbourne-based boutique manufacturer.
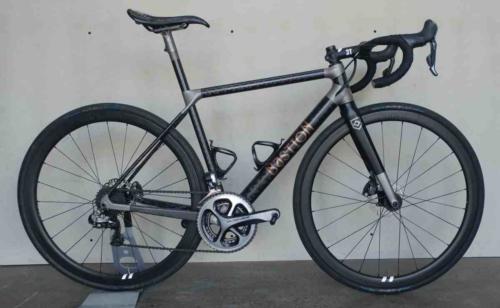
The Bastion stem is available to order now, requiring a lead time of six to eight weeks. In keeping with the stem, the cranks are customizable, with crankarm lengths available from 160mm to 180mm, while the handlebars are individually sized for the rider as well.
#Bastion bikes pro#
In FEATURED ARTICLES, LATEST ARTICLES, THE DOUBLE DIAMONDīastion Cycles has created the world’s most expensive 3D-printed stem that costs a staggering $1,399.00.Īccording to Bastion, its new stem is made from Ti6AI4V/Grade 5 titanium, which is designed to work specifically with Argon 18’s Electron Pro track frame.īastion says the stem is available in a number of stack heights, and in lengths up to 160mm with an angle of +17/-17 degrees.Ĭreated in collaboration with Cycling Australia, the stem was developed to be used by the Australian national track cycling team at the 2020 Tokyo Olympic Games.Īdditionally, Bastion has also created a titanium track crank, along with a far-flung, integrated titanium “double-drop”’ handlebar, which the Australian company says offer “aerodynamically superior with class leading stiffness” and “several riding positions that improve control and stability as well as aerodynamic performance”.
